Health & Safety
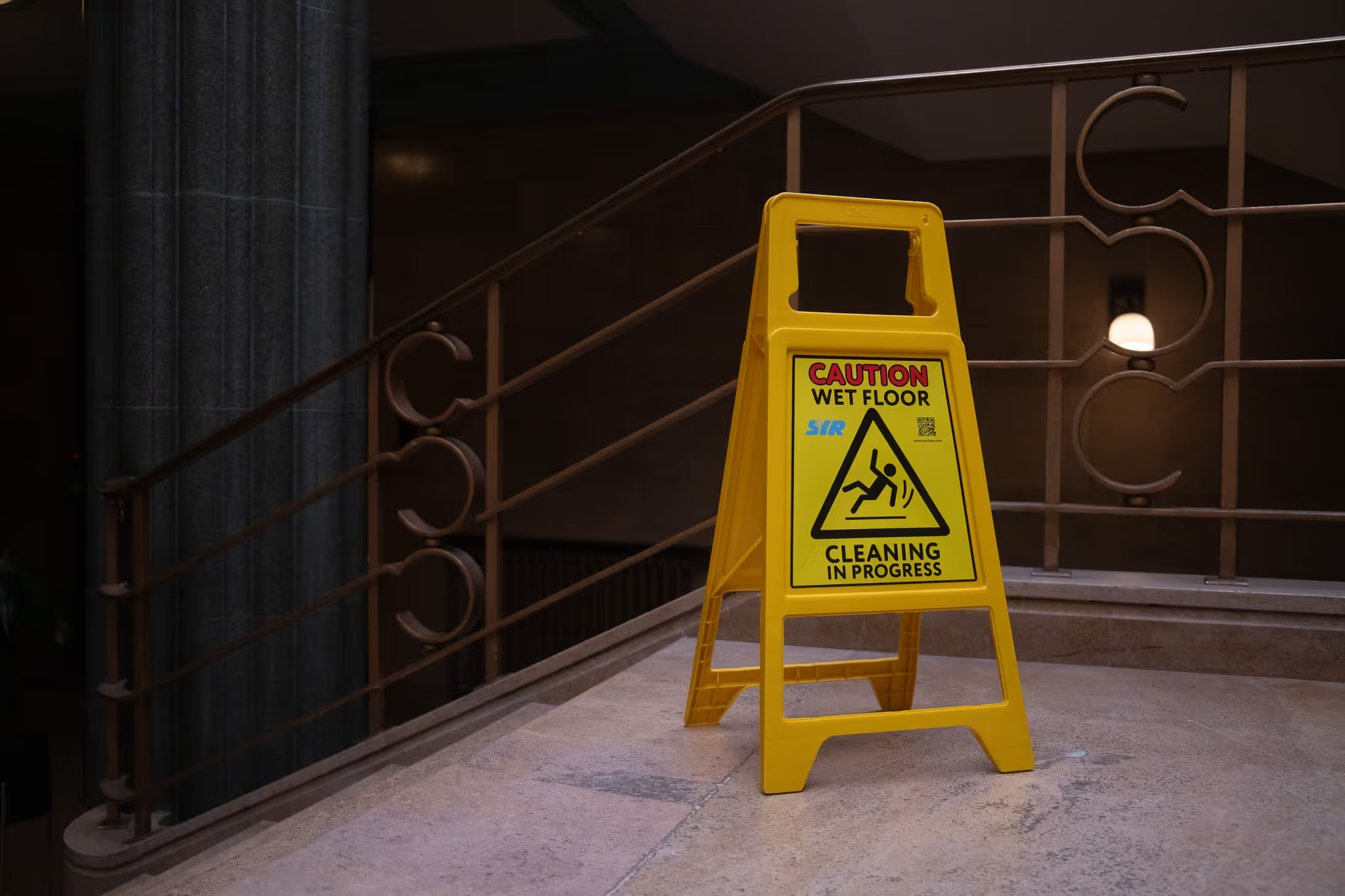
Our Priority is the Health, Safety and Wellbeing of our Staff & Clients
“The other big factor in choosing Cleanology was that staff were given relevant training, to include Health & Safety.”
Office Manager, Arts & Business (A&B)
“The other big factor in choosing Cleanology was that staff were given relevant training, to include Health & Safety.”
Office Manager, Arts & Business (A&B)
An outstanding health & safety record
To drive a positive health & safety culture, Cleanology believe commitment and active leadership must be demonstrated at senior management level. That’s why our HR Director is qualified to NEBOSH level and has oversight and overall responsibility for effective management, drive and delivery of all Health and Safety.
Our key Health & Safety statistics are monitored on an ongoing basis at both Board and Senior Management Team meetings which involves reviewing data such as Accident Incident and Accident Frequency Rates (AIR & AFR), near misses or ill-health and absence statistics. This ethos is replicated throughout all our management team, with our Area Operations Managers, Regional Operations Managers and Key Account Managers, all being qualified to IOSH standard.
In line with our ISO9001 and Safe Contractor accreditations, all managers are required to report accidents, injuries and near misses to the HR team who record and follow-up as appropriate.
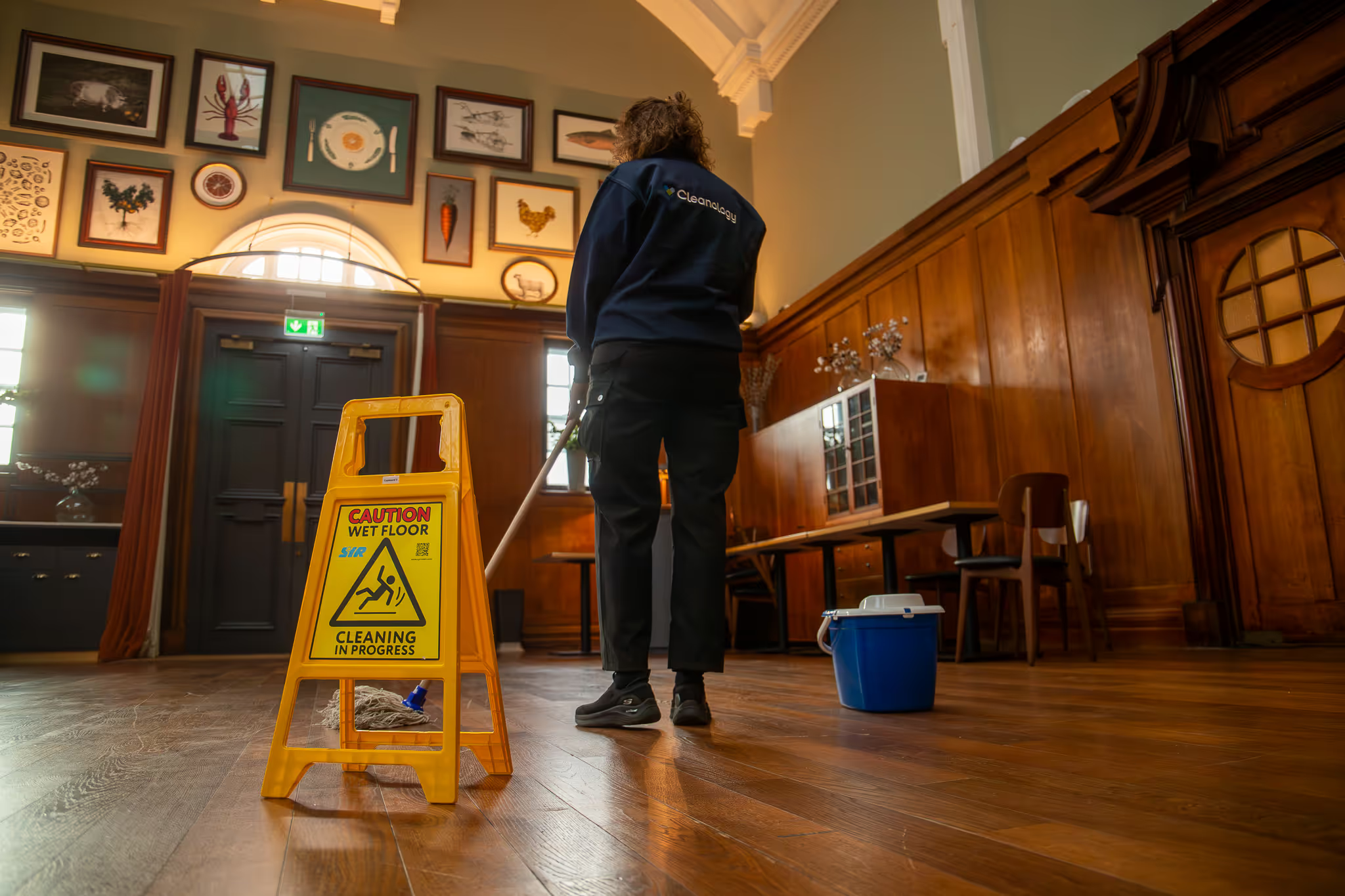
We ensure that all staff...
All employees go through our Induction process when they join the company, this includes a section on Health & Safety and how it affects our team. On the first day of a new contract employees will undergo our First Day Training Record on the site in which they will work. A major part of this training is on Health & Safety including what to do in the event of a fire or other emergency, how to get access to first aid, accessing the Site Folder including RAMS and COSHH information. COSHH information can now also be accessed via QR code. The First Day Training Record is refreshed annually.
To ensure our employees read and understand the necessary safety data sheets, we underline the importance of this at induction, explaining how to read the sheets correctly and ensuring they fully understand them. We provide regular refresher training on this as necessary. We have also made the information more easily accessible, by introducing QR codes, to encourage employees to read the information fully.
All employees are provided with PPE if required for their role, which includes gloves as a standard across all sites. Over and above this, our RAMS and COSHH processes are used to identify any specific PPE requirements required for tasks at an individual site.
Cleanology has a multitude of Risk Assessments & Method Statements (RAMS) for standard daily cleaning tasks such as vacuum cleaning, dusting, kitchen cleaning, washroom cleaning, glass & window cleaning, mopping etc. The RAMS are held in a Site Folder, which is specific to the customer location. The Regional and Area Operations Managers have responsibility for assessing the requirements of the individual site and identifying any exceptional tasks outside of the standard RAMS.
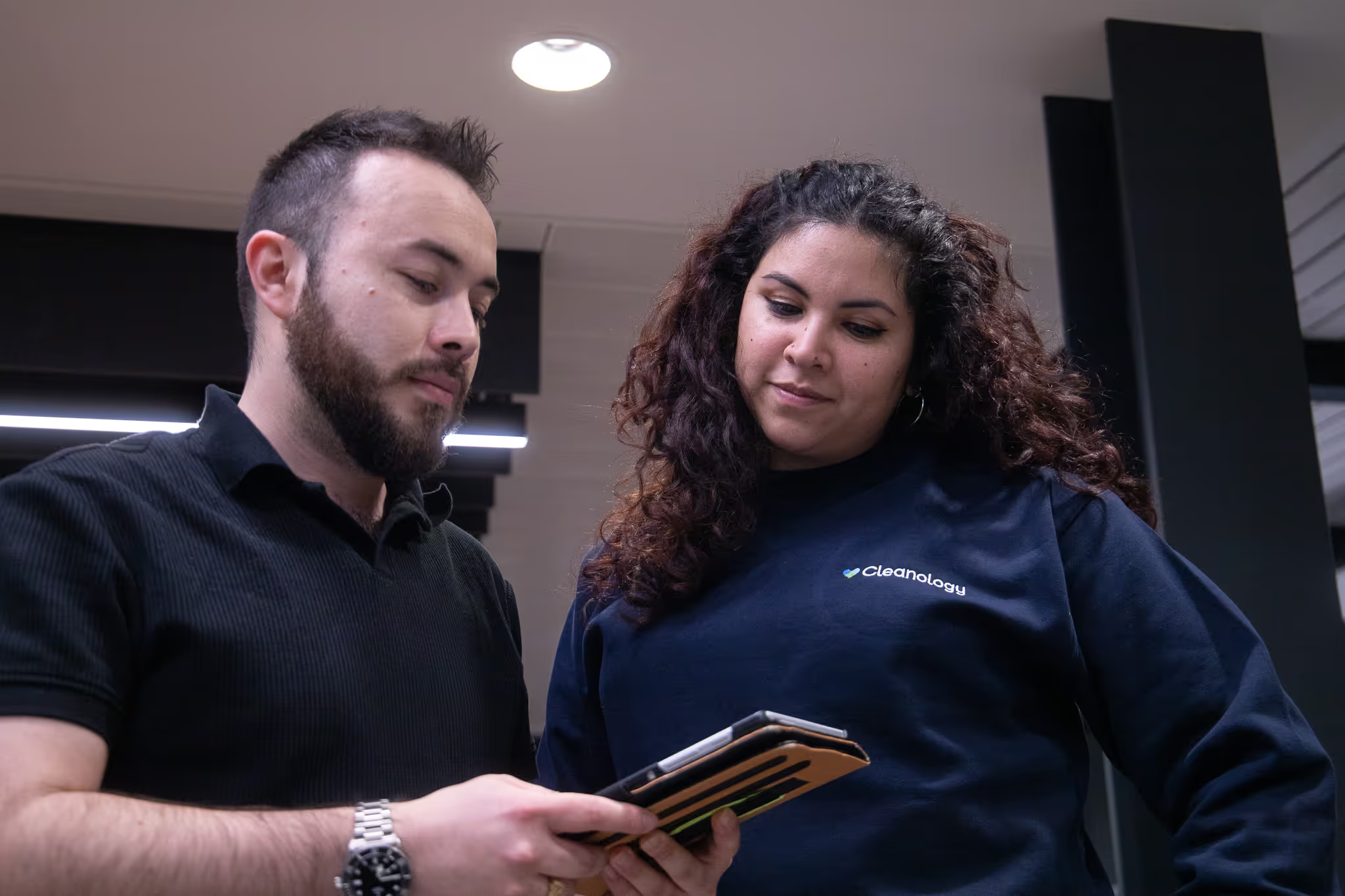
Awards & Accreditations

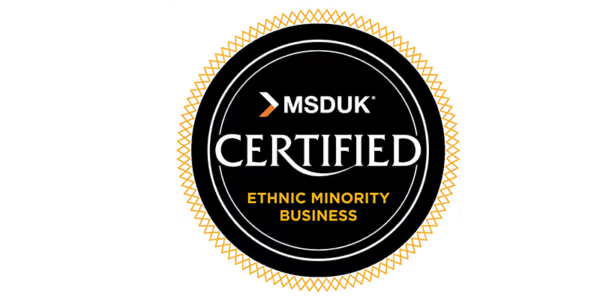
.png)
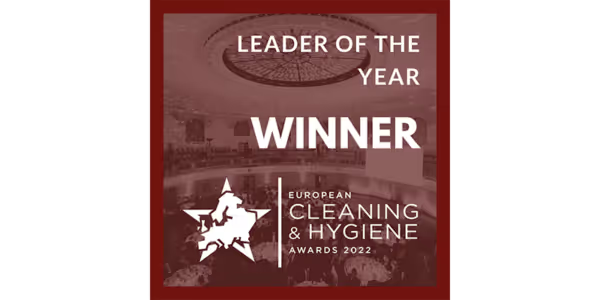
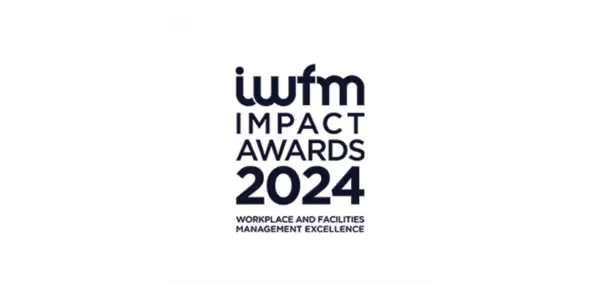
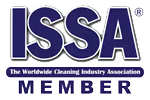
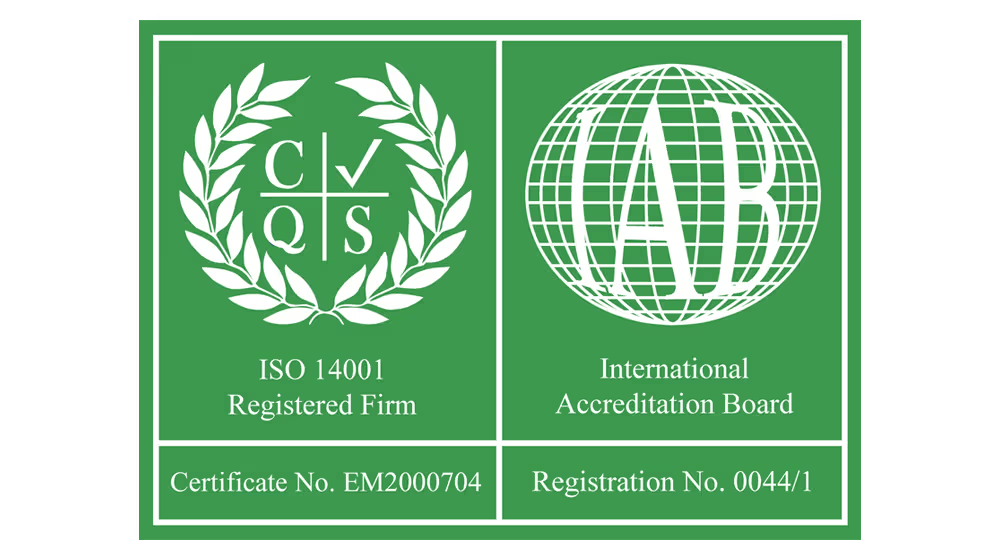
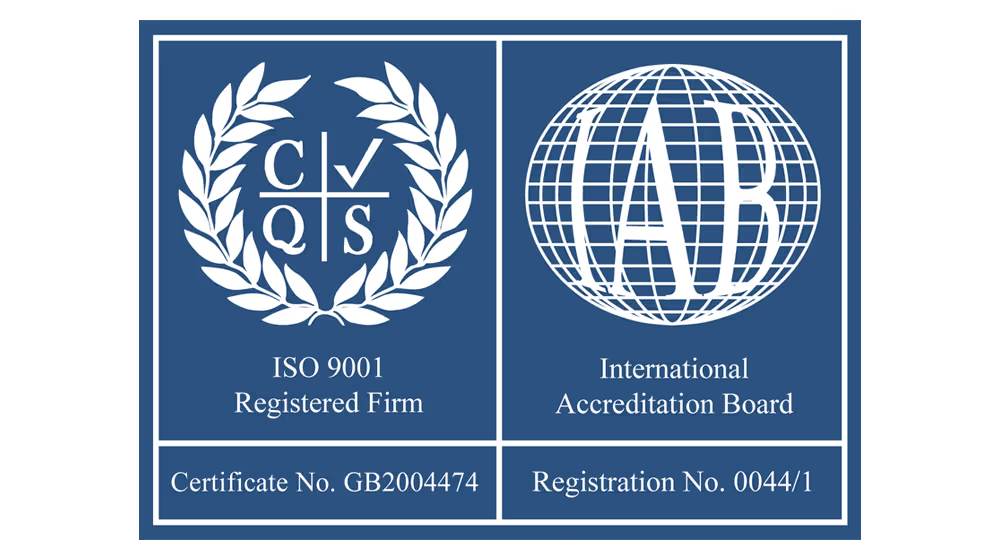

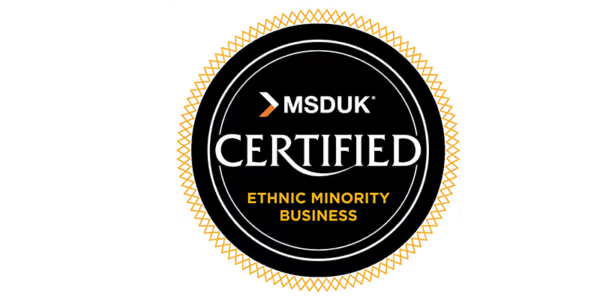
.png)
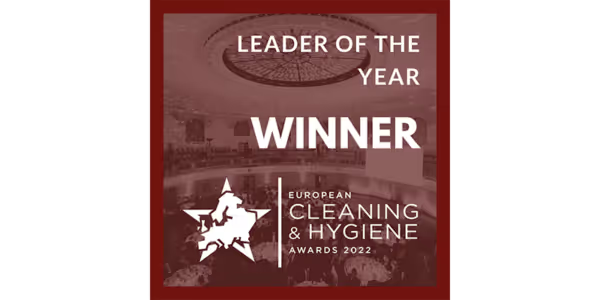
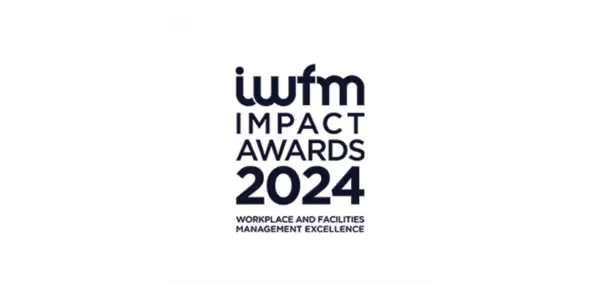
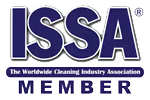
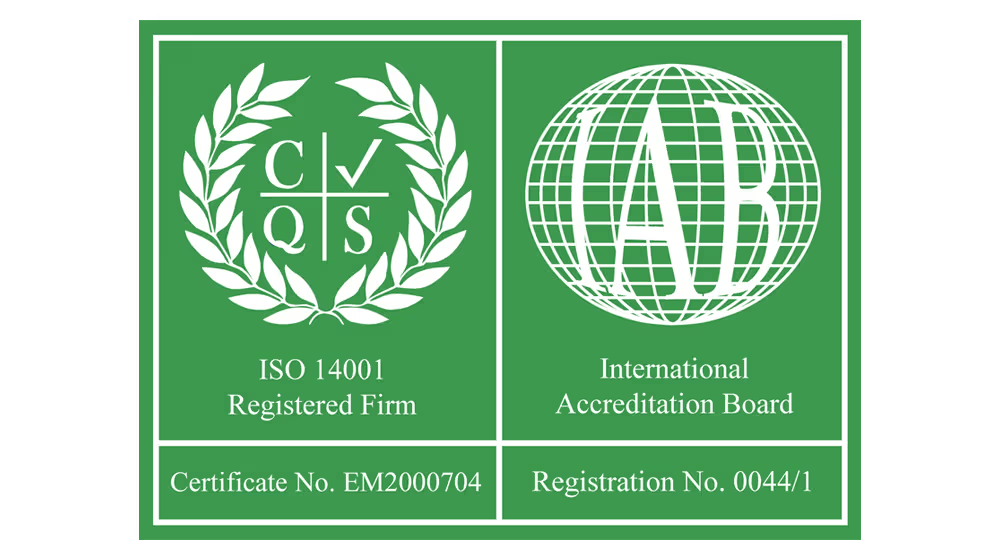
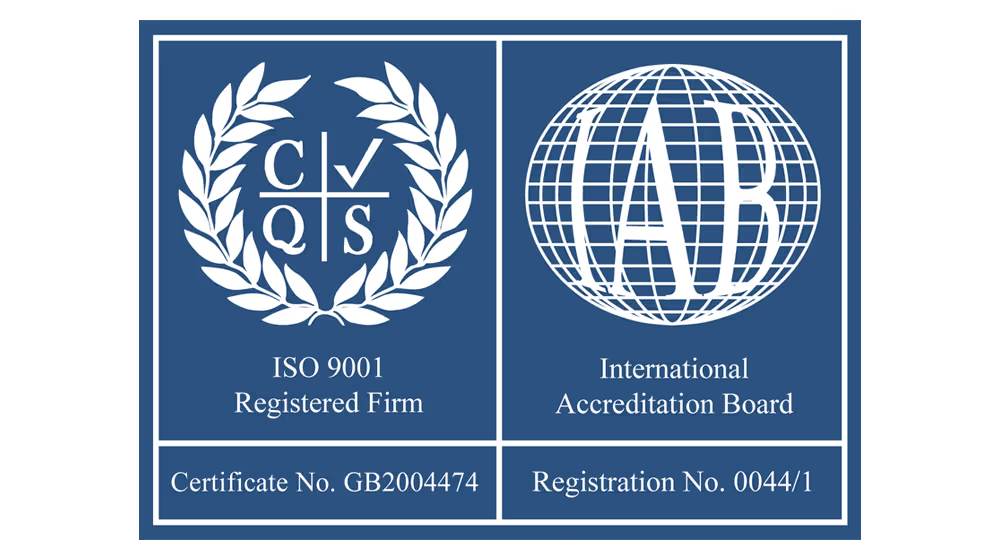